Envision
Information HIJACK, how Maintenance is deprived of Asset condition Data.
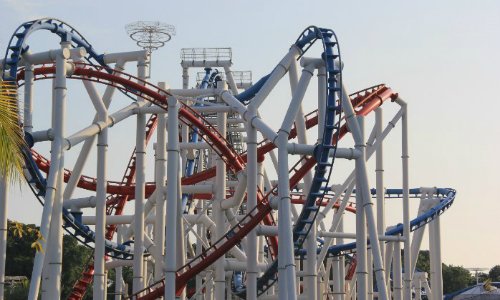
In any large scale Manufacturing or Process industry facility every system is integrated and automated. Typical Automation system would be a SCADA or DCS or fully integrated system with MES and extensive Historian.
The information stored, processed or analyzed comes from these automation systems can be classified as production process parameters, equipment performance parameters and material flows, emissions or discharge parameters. Prime custodians and consumers of this data are Production or Operations teams. Most of the time the information available for maintenance team is very limited to the extent of Alarms or events related to equipment performance or break downs. Production and Operations team would consume this information to best possible extent to accomplish their production targets as they will have access to HMI’s, Historians and MES systems with immediate access to optimize the production outputs.
When it comes to Maintenance team the information available is very much limited to alarms and events. Interestingly events or alarms are trigger points or thresh hold parameters like pressure, temperature, heat, flows, vibrations or any other sensor data; which alarms that there is equipment performance mismatch. This requires attention of Maintenance team for fixing the problem to push the respective parameter away from thresh hold.
Prime objective of condition based maintenance is not met as these alarms or events provides very limited information. Information like the time taken to reach threshold is not available, information about the associated actors which push the equipment to out of optimum performance zone is never available for maintenance Engineer for analysis.
Ideally for Maintenance Manager requires integrated view of Equipment break downs, failure history, frequency of alarms/events related to failure, time taken to reach point of failure state, history of associate actors which push the prime parameters to the threshold. This integrated view will help the engineer to apply best methods to improve the asset performance and reduce the down time.
In spite of mature of Automation of production systems and best IT systems in EAM, there are very few implementations where Integrated EAM system with dedicated Historian of equipment performance data available for maintenance teams for decision making.
Envision provides solution for seamless integrated view of best of the breed integrated Condition monitoring Historian integrated with CMMS/EAM solutions like Maximo, SAP PM, Oracle EAM and other CMMS solutions for every industry.
The opinions expressed in this article are the author’s own and do not reflect the view of the organization he is connected with.
Talk to us today to know how our solutions can accelerate your digital transformation
Let's Talk